CASE STUDY – ASHP – AFFORDABLE COOPERATIVE, MANHATTAN
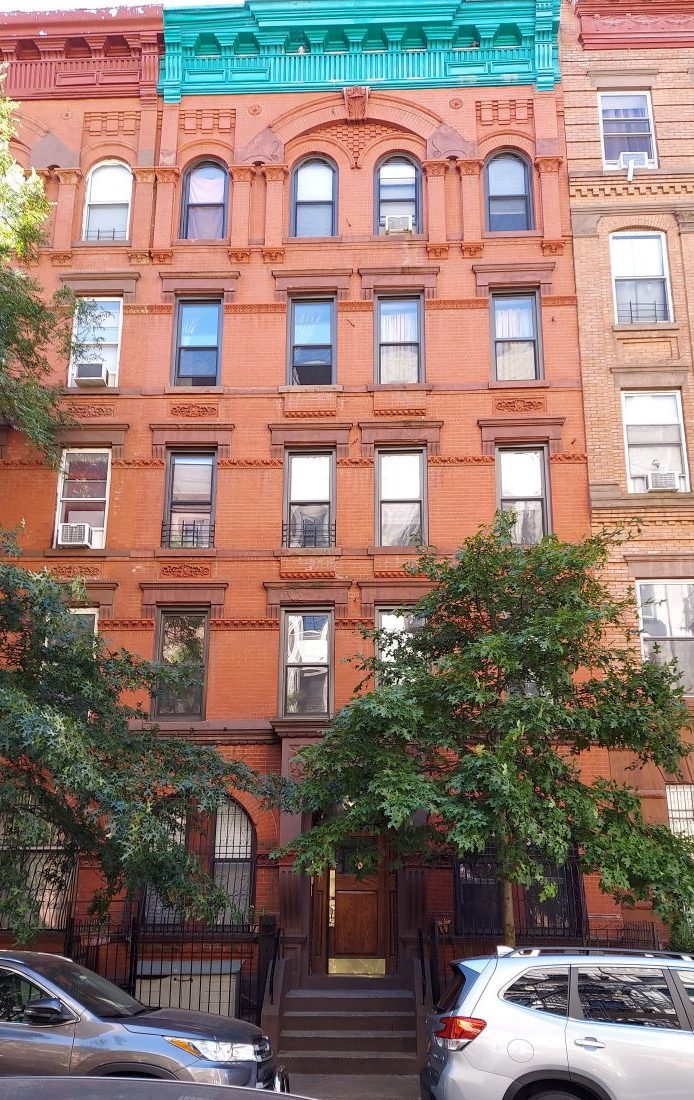
This HDFC 9,700 sq. ft. multifamily building has 10 units in a 5-story walk-up. There are at least 40,000 similar buildings in New York City.
Services
IGP, acting as Efficiency Advisor in the NYC Retrofit Accelerator, assisted this moderate income multifamily cooperative on the Upper West Side to participate in an important Case Study to convert a typical oil-fired steam-heated building from fossil fuels to electric high-efficiency air source heat pumps (ASHP).
IGP had been assisting this coop Board since mid-2018 to consider space heating alternatives to their oil-fired steam boiler. IGP educated them on NYSERDA’s ASHP incentive program, introduced them to some ASHP installation contractors, and reviewed their installation proposals. In December 2018 IGP introduced the Board to one experienced ASHP installer, who did a site visit and provided a comprehensive proposal in early 2019, but the project would cost more than they had anticipated.
In April 2019, Tom Sahagian asked IGP if we knew of any buildings that would be interested in participating in a new ASHP Case Study pilot program. His criteria for selecting a candidate building included the characteristics of this multifamily building:
- 10 or more units
- Direct metered for electricity
- Oil-fired boiler
- Steam heating distribution system
IGP introduced members of the Board to Tom Sahagian, and the rest is history. See the February 2, 2021 article in Habitat Magazine “Upper West Side Co-op Steps into the Electrified Future”.
Case Study
Partnering with Ian Shapiro, PE from Taitem Engineering, Tom reached out to a well-known ASHP manufacturer, to transform this typical steam-heated building into a more comfortable, efficient building with heat pumps.
Property Information:
- Market Type: Affordable Multifamily Cooperative, Manhattan
- # of Buildings: 1
- Year Built: 1926
- Building Area: 9,700
- Total Units: 10 residential
Project Results:
This Case Study for this project was presented at the NESEA BuildingEnergy NYC 2020 virtual conference on September 24, 2020.
During this presentation Tom reviewed the project design process, installation process, lessons learned, and the environmental, energy, and comfort impacts to the building and its occupants. The residents installed either wall mounted or floor mounted ASHPs, as shown in the photos. The layout of this 10-unit “railroad” layout apartment building is very typical in New York City.
As Tom explained in the video, the shareholders decided to keep the oil-fired boiler to produce domestic hot water (DHW). In the future, as more buildings install electric ASHPs for heating, the electric peak demand period may also be in the winter. Keeping the oil-fired boiler to provide steam to the radiators that were not removed, may help to shave these peak electric demands during the heating season.
The Top 10 Lessons Learned
- Someone should oversee the job on behalf of the building.
- There will always be surprises – electric wiring issues and unexpected air leakage.
- Airsealing is an integral and mandatory part of the job – Perform a Blower Door Tests if possible.
- A heating/cooling load calculation is strongly recommended.
- An electrical upgrade is not always necessary.
- Plan for residents’ temporary relocation.
- Nail down all the residents’ preferences before equipment is ordered.
- Establish flare connection, pressure test and vacuum test protocols before installation.
- Avoid brazed joints if at all possible; don’t hide flared or brazed joints inside walls.
- Asbestos can be a wild card.
The next year will be spent gathering data.
The photos help to tell the story.
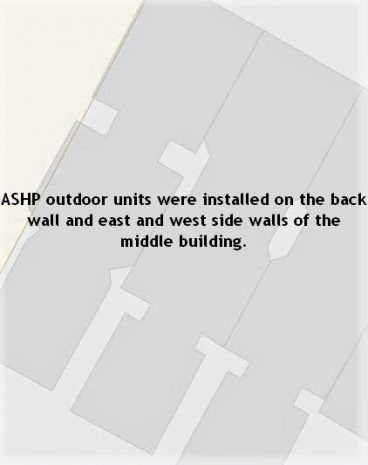
This is a typical 25ft. by 90ft five-story walk-up, 9,700 sq. ft. pre-war apartment building with ten units, built in 1926. There are at least 40,000 similar buildings in New York City. The data from this approximately 10,000 sq. ft. building can be extrapolated and applied to a theoretical 100,000 sq. ft. multifamily building. The energy savings with electric ASHPs can reduce carbon emissions significantly, compared to fossil fuel fired boilers.
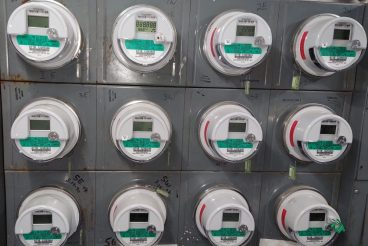
The Con Edison direct electric meters in the basement service each of the ten units and all common areas.
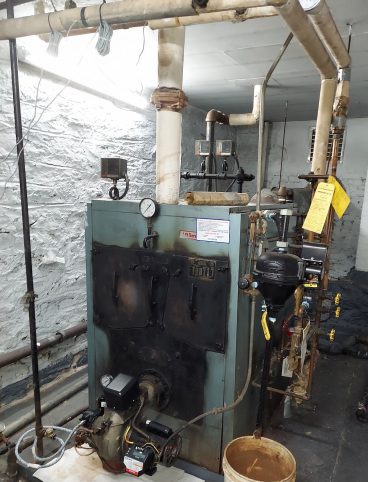
The building is keeping its No. 2 fuel fired steam boiler as part of a possible Demand Response strategy if Con Edison’s peak electric demand shifts to the winter.
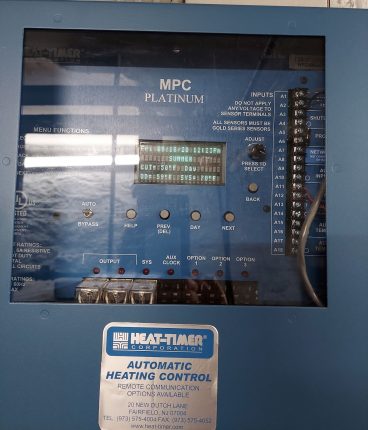
The Heat Timer boiler control system often leads to over heating and open windows because it is difficult to balance a 1-pipe steam system.
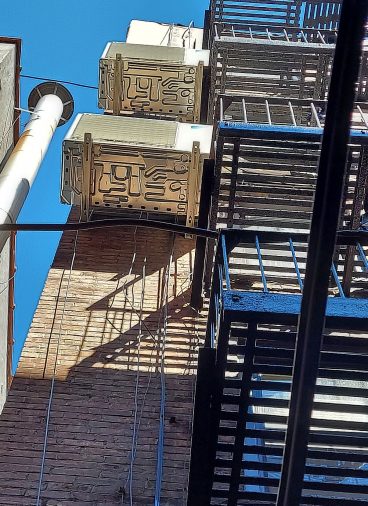
These two ASHP outdoor units were installed on the back wall next to the fire escape.
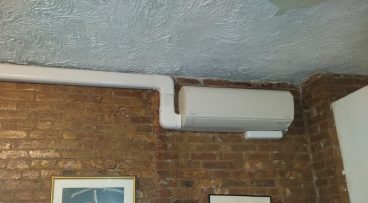
ASHP indoor unit with condensate pump at bottom. The refrigerant and electric lines extend to the outdoor unit on the roof.
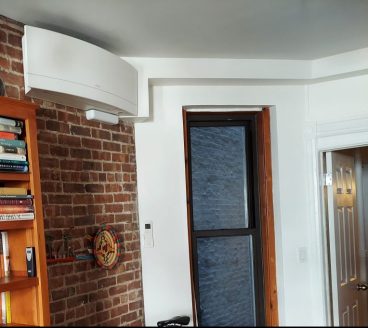
ASHP indoor unit is installed on side wall with a soffit to hide the refrigerant and electric lines extending to the back wall outdoor unit. The hand held remote control is mounted on the wall.
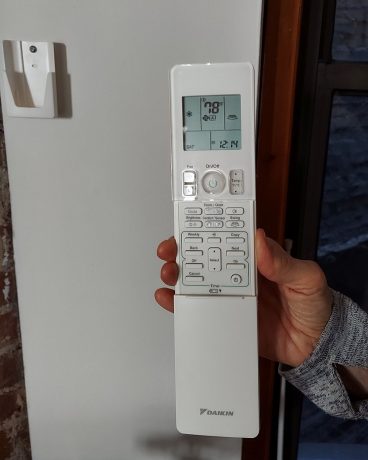
Each hand held digital monitor, which can be hung on the wall, controls the operation of each ASHP in the apartment. The residents can also program the ASHPs remotely by using an app on their phone. One big advantage of ASHPs is that they can be programmed to satisfy the comfort level of each resident. Overheating the building is avoided by having localized control.
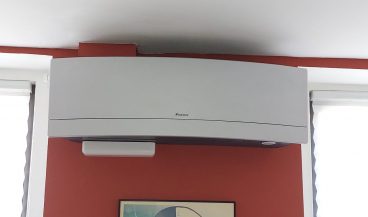
This ASHP indoor unit and condensate pump was installed on the building’s front wall. A small soffit hides the refrigerant and electric lines that go above the ceiling and extend to the outdoor unit on the back wall of the building.
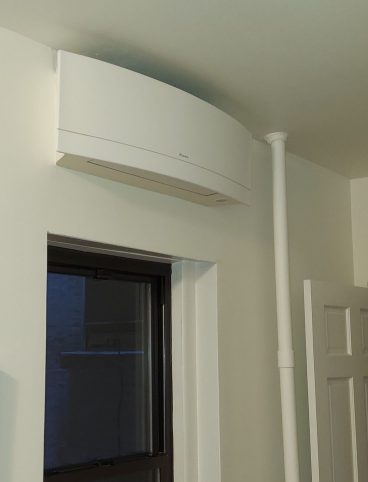
This ASHP indoor unit, installed on the back wall does not require a condensate pump inside, because the condensate drains directly to the outside.
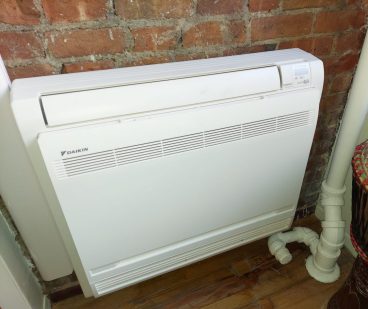
This unit replaced the one-pipe steam radiator with the floor model ASHP. Note the capped steam supply line.
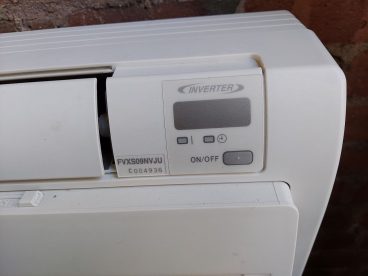
The floor model’s digital display is on the unit and can also be programmed remotely, using an app on the resident’s phone.
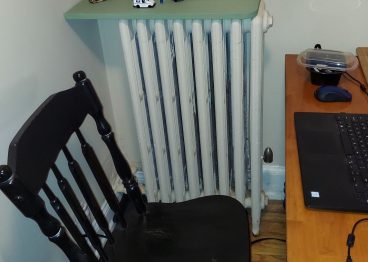
Each apartment kept the original one-pipe steam radiators in the same room as the ASHP to reduce possible peak electric loads in the winter.
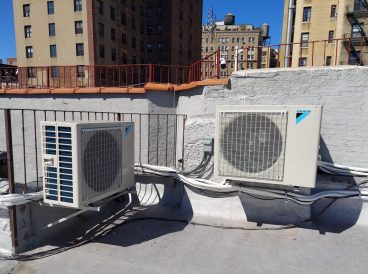
Two ASHP outdoor units, one for each apartment, are installed with brackets on the roof’s parapet wall. They are located about two feet off the roof to avoid snow in winter and also allow for a future roof replacement. Other outdoor units are installed on the side and back walls of the building.
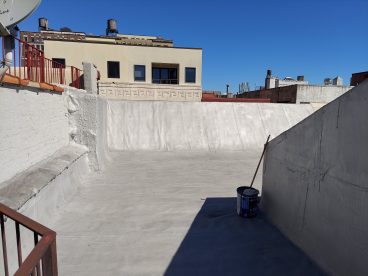
Putting only four outdoor units on the roof, with the rest on back and side walls, frees up roof space for possible Solar PV.
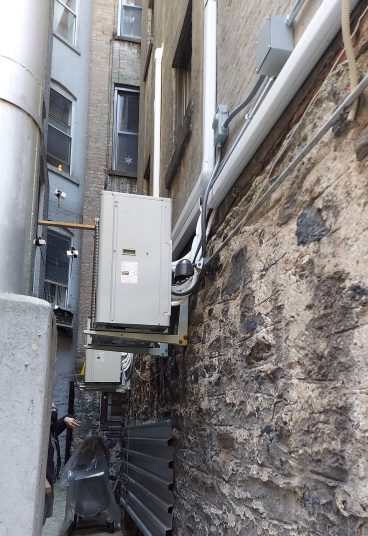
Two ASHP outdoor units on west side wall. Note the electric and refrigerant lines going into the west side mid-level apartments.
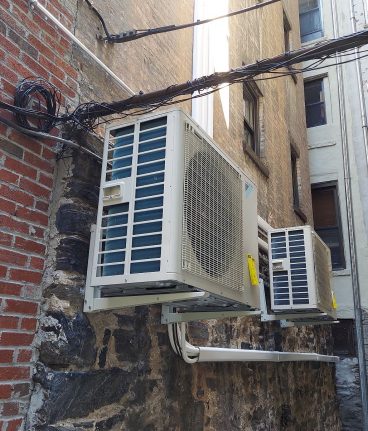
These ASHP outdoor units on the east side wall serve the mid-level apartments on the east side of the building.