CASE STUDY – MULTIFAMILY COOPERATIVE
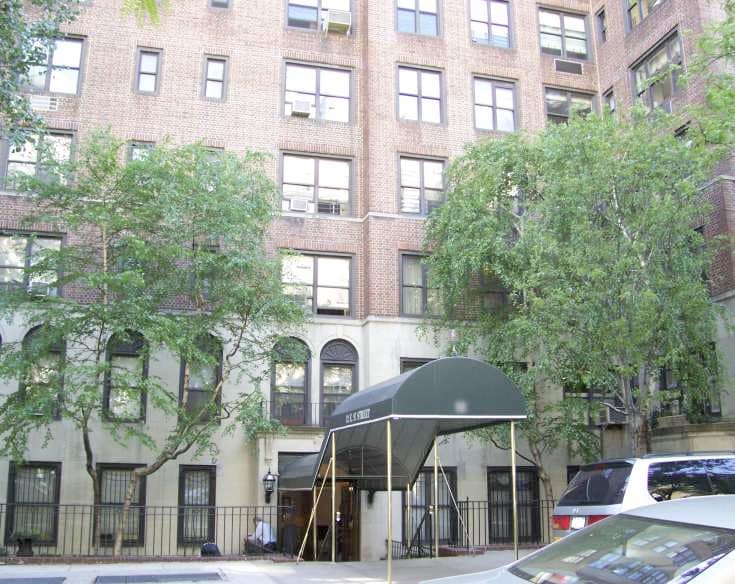
Services:
IGP, acting as Owner’s Representative to this Upper East Side cooperative, planned and managed one of the first Fuel Conversion Projects in New York City after the passing of LL43/10, which required buildings to stop using No. 6 oil.
Property Information:
- Market Type: Multifamily Cooperative on Upper East Side of Manhattan
- Building Area: 118,008 square feet
- Total Units: 107: 106 Residential, 1 Professional
- Built: 1928
- Original Heating Fuel: No. 6 oil
- Projects: LL84/09, LL87/09, LL43/10 Fuel Conversion
- Incentive Program Approved: NYSERDA Multifamily Carbon Emission Reduction Program
Fuel Conversion Project Results:
IGP provided fuel conversion Project Management, Energy Efficiency and Financial Advisory services. Through a competitive bidding process, IGP assisted the Board in selecting each contractor, collaborated with the energy engineering and design engineering teams, the building’s property manager and operations staff, Con Edison, the NYC Department of Buildings and NYSERDA.
The fuel conversion project proved to be complex and time-consuming. IGP had to advocate on the Board’s behalf to obtain a special positive ruling from Con Edison for additional low pressure gas service in the Carnegie Hill area at no extra charge for connecting the building to the main gas line. IGP also assisted the Board to access funding from NYSERDA’s Multifamily Carbon Emission Reduction Program to help pay for the design and construction of this project. IGP managed this project over a two-year period; visited the site regularly with the prime contractor and design engineer, and continually updated the Board with written reports to avoid any surprises.
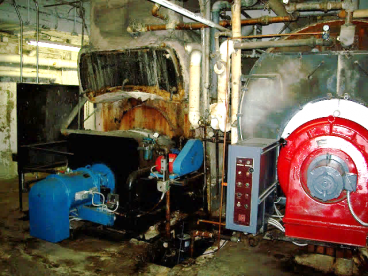
Before the Fuel Conversion: On the left, the original 85-year old coal boiler, once converted to use No. 6 oil, was removed. On the right, the 35-year old boiler using No. 6 oil, was well maintained and still in good condition internally. The owner decided to refurbish it as part of the fuel conversion project.
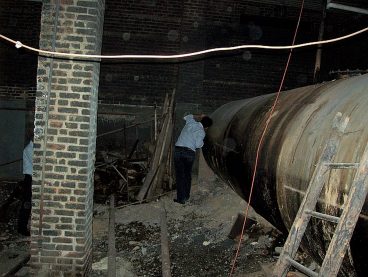
We removed the old No. 6 oil tank which was resting on the dirt floor. The floor was cleaned up and debris was removed. In this space we installed the new gas meter room.
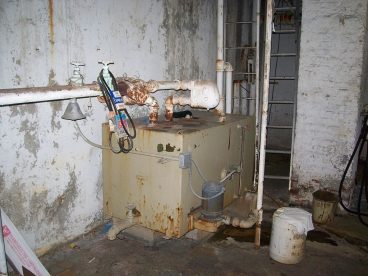
This is the condensate tank before we did the fuel conversion and upgrade of the Boiler Room.
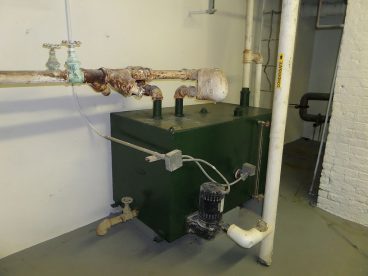
Refurbished condensate tank with insulated condensate line. This process was still under construction.
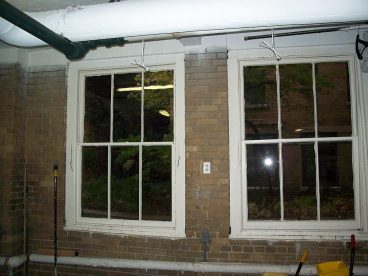
Single pane windows in the basement should be replaced with double pane windows to avoid stack effect and heat loss in the building.
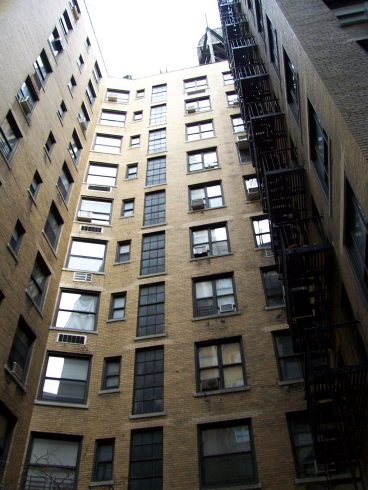
Note the double pane windows, upgraded from the original 1929 windows, in tenant apartments. However the coop did not replace the single pane stairwell windows because “no one sees them”. However, to really improve the building envelope, these windows should be replaced with double pane windows to reduce heat loss during the summer and heat gain during the summer.
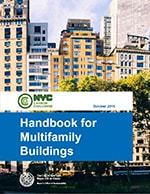
LL87/09 Project Results:
- This Case Study has been included the NYC Carbon Challenge Handbook for Co-ops and Condos since 2013.
- Upgraded common area lighting
- Installed occupancy sensors in common areas
- Distributed new CFLs for free to tenants
- Replaced all steam traps in tenant spaces during the summer
- Installed new dual fuel burner, new stainless steel chimney liner
- Upgraded boiler operating systems
- Installed new gas-fired domestic hot water system
- Removed original 1930s era coal boiler; & 6000 gallon No. 6 oil tank
- IGP managed the projects until completion in May 2013
See the NYC Carbon Challenge for Multifamily Buildings, October 2016, page 41 for this Case Study.
“Our co-operative retained IntelliGreen Partners in connection with our conversion from #6 fuel oil to gas, and our compliance with NYC and NYS benchmarking and energy conservation mandates. I can say unequivocally that we benefited immeasurably from IGP’s involvement in these complex projects, and I shudder to think how our dealings with Con Ed and the City would have turned out without their guidance. IGP’s technical knowledge, service provider experience and relationships, attention to detail, and skillful management were absolutely critical to completing these projects successfully.” John Slattery, Treasurer of the Co-operative Board.
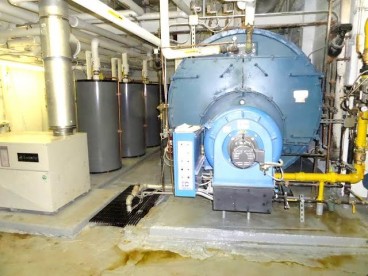
After the Fuel Conversion: The boiler room has a refurbished insulated boiler with new dual fuel burner (No. 2 oil and natural gas). The new Lochinvar water heater with three storage tanks allow the boiler to be turned off, saving wear and tear, during the non-heating season.
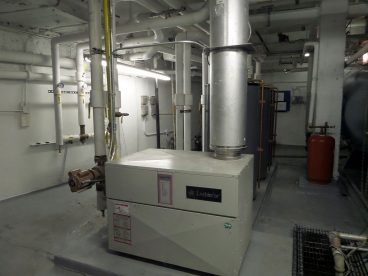
We installed a new Lochinvar DHW Heater to heat the water during the non-heating season. This practice will allow the boiler to rest during the summer and have a longer useful life. It is also more energy efficient to use the DHW heater in the summer rather than use the large Scotch Marine Boiler just to heat hot water.
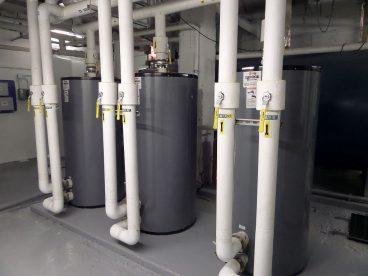
The new DHW heater with three new storage tanks.
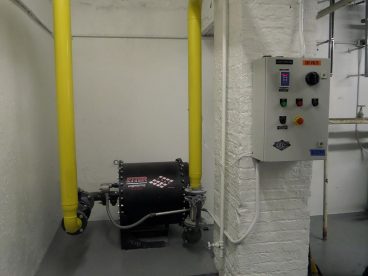
We had to lower the gas pressure coming into the building from the main gas line, and then use this gas booster to increase the pressure for the Scotch Marine Boiler.
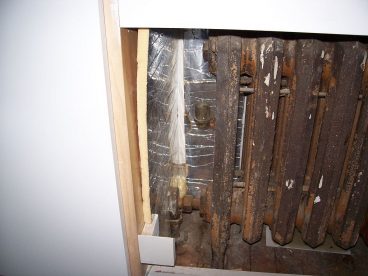
During the LL87 process we discovered two-pipe steam radiators with old air vents on them, which had to be removed. Insulating the back side of the radiator can reduce drafts in winter.
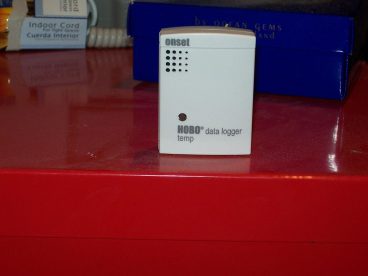
As part of the LL87 Energy Audit we did a temperature data logger study to see what part of the building was over heated or under heated, in an attempt to improve balancing the heating distribution system.
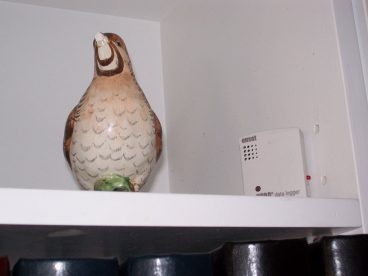
Note the tiny Hobo temperature data logger used to help balance the heating distribution system. We left the data loggers for three or four weeks to collect as much data as possible during the winter months.
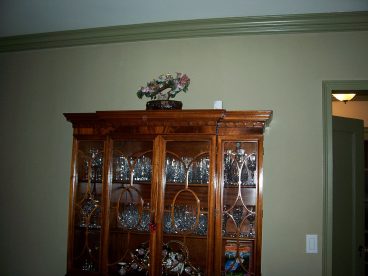
Tenants didn’t mind having these temperature data loggers in their apartments for a month or so. Note how small and unobtrusive they are.