CASE STUDY – MULTIFAMILY COOPERATIVE, MANHATTAN
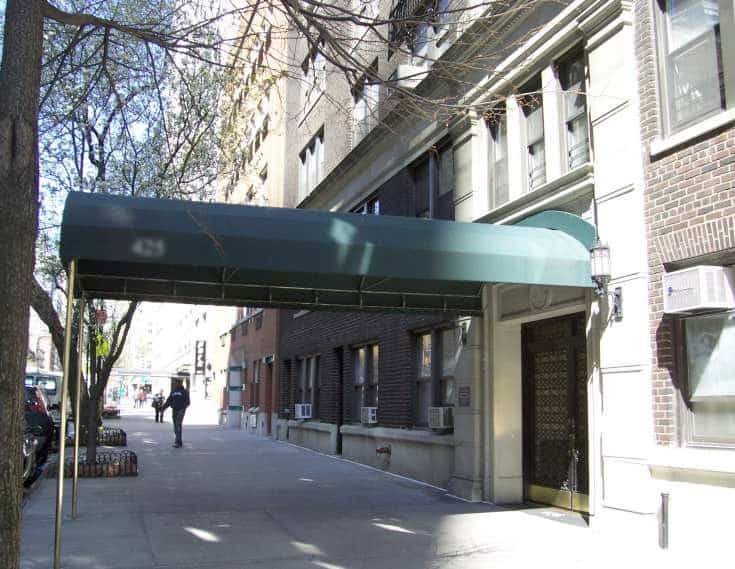
Services:
IGP, acting as Owner’s Representative to this Upper East Side multifamily cooperative, planned and managed one of the first Fuel Conversion Projects in New York City after the passing of LL43/10, which required buildings to stop using No. 6 oil. IGP also led the engineering team to complete LL87 Energy Audit & Retro-commissioning due in 2013.
Property Information:
- Market Type: Multifamily Cooperative on Manhattan’s Upper East Side.
- Building Area: 118,351 square feet
- Total Units: 74: 72 residential; 2 professional
- Built: 1929
- Original Heating Fuel: No. 4 oil
- Projects: LL84/09, LL87/09, LL43/10 Fuel Conversion
Fuel Conversion Project Results:
IntelliGreen Partners provided fuel conversion Project Management, Energy Efficiency Consulting and Financial Advisory services to this multifamily cooperative:
- IGP revived a fuel conversion project for which the incorrect Load Letter had been filed with Con Edison.
- IGP arranged for and submitted the correct Load Letter and immediately collaborated with Con Edison to get the project back on track in a couple of weeks.
- Through a competitive bid process, IGP assisted in selecting the design engineering firm and prime construction contractor.
- IGP collaborated with the Board, property manager, operations staff and Con Edison, to assist the Owner in complying with Local Law 43/10 phasing out the use of No. 4 oil by converting its boiler to dual fuel (No. 2 oil & natural gas).
- IGP visited the site regularly with the property manager, prime contractor and design engineer and continually updated the Board with written reports to avoid any surprises.
- IGPe coordinated our fuel conversion project with the building engineer’s LL11 Facade Project, also due in 2013. We made sure the crew installing the new stainless steel chimney liner did not conflict with the LL11 facade crew.
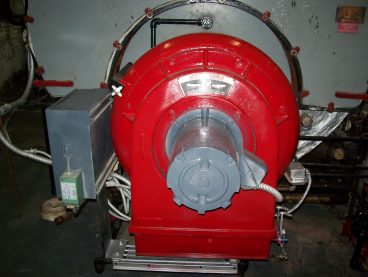
Original No. 4 oil burner which was replaced with a dual fuel burner using No. 2 oil and gas.
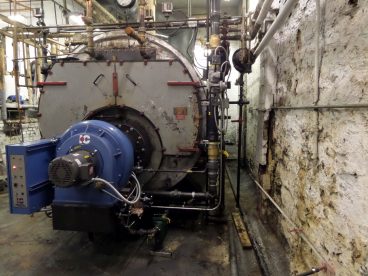
New dual fuel burner installed on 1987 boiler with still more refurbishment required to bring the Boiler Room up to current Code.
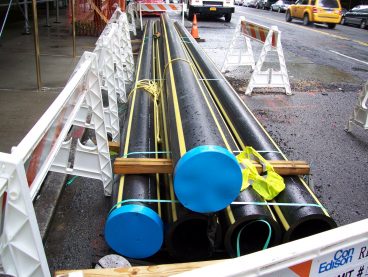
Con Edison installs new gas lines in this Upper East Side “Area Growth Zone” for new gas customers who are switching from No. 4 or No. 6 oil to gas to comply with LL43/10.
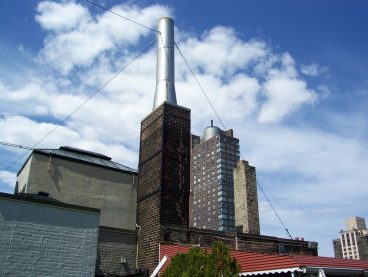
New stainless steel chimney liner installed now that gas is being used. Previously the boiler used only No. 6 oil so a liner was not required.
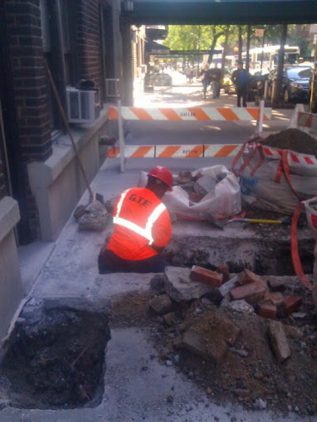
Project Results (continued):
LL43/10: Con Ed installs new gas line to the property line of the building.
- IGP prepared the Scope of Work and Request for Proposals for the engineering design and construction administrationLL43/10: Con Ed installs new gas line to the property line of the building.
- IGP assisted in the selection of the Prime construction contractor through a competitive bid process
- IGP managed the project until completion in November 2013.
LL87 Energy Efficiency Measures Recommendations:
- Lighting
- Adjust outdoor astrological time clock
- Replace T8 and T12 fluorescent magnetic ballast lighting with LED lighting with electronic ballast in the following areas:
- common areas
- basement corridors and common areas
- laundry room
- stairwells
- Replace 150 Watt flood lights on exterior of the building with 17 Watt LEDs
- Replace incandescent bulbs with 2 Watt LED candle lights in lobby candelabras
- Install occupancy sensor/photo-sensor lighting controls where feasibile
- Make domestic hot water (DHW) temperature adjustments
- Install thermostatic steam valves (tenant radiators)
- Install new Energy Management System to operate boiler on average indoor temperature, not outdoor temperature
- Replace pressuretrol with vaporstat to allow for more precise control at no more than 2psi
- Insulate uninsulated hot water, cold water and steam pipes
- Convert fuel from No. 4 oil to dual fuel (No. 2 oil and gas)
- Weather-strip exit doors and around windows
- Insulate air conditioner sleeves (tenants)
- Air conditioning upgrades to Energy Star (tenants)
- Install window films to reject heat in daytime and reduce glare at night
- Upgrade single pane stairwell windows with clear double pane windows to enhance lighting and reduce heat loss
- Install a separate gas High Efficiency Domestic Hot Water (DHW) heater
Note: A total potential savings of $226,903.00 of independent energy efficiency measures were identified. The simple payback for all measures was 6.0 years.
“I’d also like to take the opportunity to say thank you for your efforts on the corporation’s behalf. It was a pleasure working with you and IGP. I think the boiler conversion process went very well, and your knowledge, initiative, and energy were major contributors to that. We look forward to benefiting from lower energy costs for many years to come, not to mention the building’s reduced contribution to atmospheric pollution.”
Treasurer of the Co-operative Board
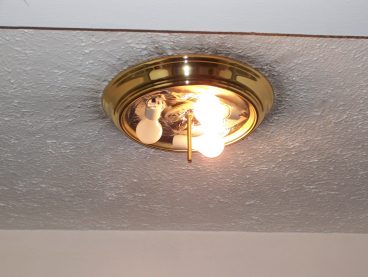
Replace corridor incandescent light bulbs with LEDs with sensors.
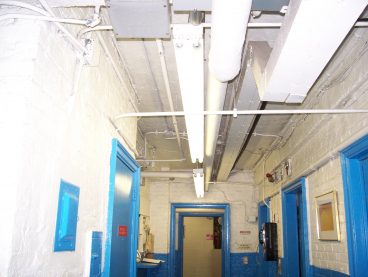
Replace 8 ft T12 fluorescent lights in basement with new LED fixtures
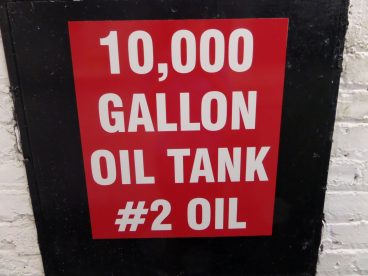
IGP arranged to have the old No. 6 oil tank and tank room cleaned and repaired before introducing No. 2 oil. The primary fuel will be Con Edison natural gas.