Radiator Retrofit Project for a Mixed-use Building
Mixed-Use Rental Building – LL87 “Early Compliance” and Radiator Retrofit Project
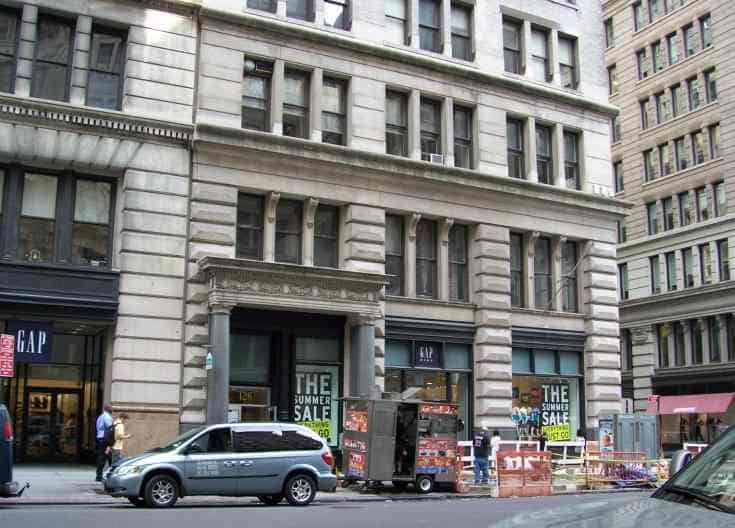
Radiator Retrofit Project
Project Results:
- Building Area: 101,549 square feet
- Total Units: 30: 15 residential; 14 commercial; 1 retail
- Built: 1905
- Original Heating Fuel: No. 6 oil, since converted to natural gas
- Projects: LL84/09, LL87/09
- Incentive Program Application: NYSERDA FlexTech Program; Con Edison Commercial & Industrial Program (C & I)
Services:
IGP provided project management services to assist the Owner of this mixed-use rental building in selecting the LL87/09 energy auditing team and the LL87/09 Retro-commissioning team to “comply early” in 2013, and to access funding from NYSERDA’s Flex Tech Program. IGP assisted with LL84/09 Benchmarking in 2010, 2011,2012 and 2013.
This building, also built before the steam trap was invented for buildings, had what appeared to be a three-pipe radiator heating system. The radiators had a mix of air vents, steam traps, and sometimes both on the same radiator. IGP researched the history of the building and brought in an historical steam heating expert who determined that the building had a unique three-pipe air vent system known as the “Paul System”, the first vacuum steam heating system in America.
The Paul System consists of a supply pipe, a return pipe and a third 1/4 inch copper line connected to the air vent tapping on each radiator that ran back to the steam-jet powered vacuum inducing venturi box “exhauster” in the basement. Each radiator had its own return air-line. The third pipe removed the air from the system [and each radiator] before the steam is allowed to enter. The exhauster was long gone. Most of the air-lines had been disconnected and abandoned.
Working with the LL87/09 energy engineer IGP assisted the owner to develop a retrofit plumbing project scope of work and request for proposals.
Project Results:
- IGP Identified that its unique 1905 3-pipe Paul Vacuum Steam Heating System was malfunctioning.
- IGP assisted in the bid process and selection of the Master Plumber contractor.
- IGP coordinated installation site visits to tenant spaces with 100% success rate
- IGP managed the project to retrofit the radiators to be more consistent with the system’s original design intent, which was closer to the two-pipe air vent system, once the third pipe was removed.
- Installed new air vents and thermostatic radiator valves (TRVs) on each radiator, giving tenants more control over their heating so they would not have to open windows.
- Reduced the boiler pressure significantly because the steam can more efficiently reach the top floor.
- IGP managed a winter temperature data logger study of each unit to balance the heating distribution system further.
Period: 2013 – 2015